Development &
Design
Our in-house design team realizes new products or optimizes existing articles according to your wishes. Thanks to many years of experience and a lot of creativity and attention to detail, they master every project, no matter how complex. Using the latest technology, you can quickly create new designs and innovative, patentable technical solutions for our customers. Despite the high creative and mostly technical requirements, the team never loses sight of the technical feasibility and cost efficiency.
Concept & Design
Based on the specifications of the customer, our design team works out all the details of the project in close cooperation with the respective project coordinator. Together, the first design ideas and basic concepts are created, which are recorded with quick hand sketches. Already in this first step, attention is paid to feasibility and cost efficiency.
- innovative designs
- project- and collection propolsals
- solution-oriented approach
Technical Implementation
In the next step, three-dimensional models are created using the latest CAD software. Each product is constructed in detail and dimensionally. Due to the exact design, technical problems can be solved even before they occur in production. The CAD software used is precisely tailored to our production, so that our design team already recognizes the machine feasibility on the screen during implementation. In this way, the greatest possible production efficiency can be achieved during the design phase. Often it is only small changes that account for large differences in machine running times and material consumption and can drastically reduce production costs.
- CAD
- patent-protected solutions (closures, mechanisms, connection techniques, etc.)
- production-ready finalization of customer designs
- feasibility analyses during development
- file formats: STEP, IGS, SolidWorks, Catia, Rhino, DWG and DXF
Presentation
Then presentations are created with computer graphics, so-called renderings, which already present the products photorealistic. For the illustration of the designs, the design department renders small series of images with different views. Design or color variants can also be presented in a realistic way to speed up the development process for new products. In addition, functions or construction details can also be illustrated with pictures or small animations.
- presentations with photorealistic renderings
- 1:1 original scale presentations
- technical details illustrations
- animations
Prototyping
On customer request, prototypes can be produced during or after completion of the development process. Here, either a pure design pattern as a rapid prototype or a hand sample can be created, which is already very similar to the final product in shape, size, material and function. Before the start of mass production, a serial sample for the final production release can be requested.
Design Samples
Within a few hours, 1:1 rapid prototypes can be produced using our 3D printer. The models are made of a stable plastic material and correspond in shape and size to the final product. These models can help in the gradual approach to the final product and can be part of the development process. Even simple technical functions can be simulated with these first models.
- scale 1:1
- verification of dimensions
- design variants
- standardized sample agreements
- only pro rata sample costs
- transparent cost structure
Design and Functional Samples
Based on the rapid prototyping model or the CAD file, a hand sample is created. This is a single technical prototype that is largely identical to the final product. The hand sample is produced individually on special CNC machines and is used for the final check of function, feel and appearance.
- checking function, look and feel
- standardized sample agreements
- only pro rata sample costs
- transparent cost structure
Production Samples
Original metal samples are also possible within a short time (depending on machine availability). This simplifies approval processes and significantly accelerates the entire process sequence.
- approval for production
- standardized sample agreements
- only pro rata sample costs
- transparent cost structure
Production
After the production release of the samples accompanied by EMPB (first sample test report), the product goes into production. Here we have a wide range of production possibilities. Our state-of-the-art machinery meets the highest demands for precision and efficiency. A high degree of automation promises consistent part consistency and product quality with efficient time management. In particular, we master complex parts and exceptionally high-quality requirements with reliable delivery reliability and economic costs..
CNC drilling technology
Our new high-performance automatic lathes are equipped with 3m bar feeders and thus enable a 24/7 continuous production of turned parts and combined turned/milled parts with the highest precision and economic efficiency.
- CAM turning
- long- and short turning
- drilling and milling on counter spindles
- lathes with movable spindle head
- CNC turned parts in diameters from 1 to 32 mm
- production unit numbers up to over 100,000 units per day
- 3 m bar loaders
CNC milling technology
For more complex parts and the highest demands, our CNC milling machines with 3, 4 or 5 axes are available. The feeding takes place automatically by robots, which move the workpieces independently from station to station, in these processes the automatic laser system is also integrated.
- 5-axis simultaneous machining
- simultaneous turning, drilling and milling in one clamping
- 360°-degree machining, longitudinal, transverse and reverse operations
- combined turned/milled parts
- machining sizes up to 65 mm bar stock, workpieces up to 800 mm in length and 430 mm
- ideal for medical, tool, aerospace, automotive, precision engineering, jewellery and watches
- synchronous machining by tool spindle and second turret
- CAM 3D Milling
- CAM 4-axis simultaneous milling
- CAM 5-axis simultaneous milling
- simulation programs
- automatic CNC assembly by robot
Punching Technology
Punching technology enables the use of forms that are typical and cannot be achieved by any other technique. Some product or cost targets can only be achieved in this way. Punching can also be helpful for milling technology, because (depending on the workpiece), the machine runtimes of the CNC milling machines can be significantly reduced by preliminary punching and thus the overall costs and running times.
- process-reliable large quantities
- universal efficiency
- decorative components
- assemblies
- depressions and embossments in the same stamping process
Laser Welding
Our laser welding machines enable durable connections with extreme strength and aesthetic demands. Low thermal stress is exerted on the workpiece, which means that the dimensional accuracy is maintained - which is often not possible with other high-performance connections.
- high welding speed
- low thermal distortion
- all seam geometries can be displayed
- workpieces remain maximally dimensionally stable
- shorter post-processing times
Refinement
Due to our origin from the luxury industry for consumer goods, we have a lot of experience with high-quality and very demanding finishing. We reinvent ourselves for each project and enjoy the challenge of giving each customer an individual touch and an unmistakable recognition value.
Decorative Surface Treatment
Originally from the high-quality jewelry and watch sector, we have a lot of experience with the finishing of surfaces. The mechanical or manual processing of the workpieces in our company ranges from "simple" matting to machine polishes of various grades to high-quality brushing. Here it is possible for us to process surfaces completely, partially or mixed.
robotics and manual work:
- tumbled
- polished: disc centrifugal machines, vibratory grinding machines, drag grinding machines, robot polishes
- brushed: robot brushing, manual brushing
- satin: sandblasted, manual and automated
Coating
Both already surface-processed and also raw workpieces can be provided by various methods with transparent color coatings, which maintain the structures of the surface treatments. Depending on the material and customer specifications, we work with coating thicknesses of ‘Eco’ up to 10 years warranty.
- PVD (coating thickness of 'eco' up to 10 years warranty)
- gild
- silverplate
- electoplating (IP)
- galvanization
Painting/Lacquer
We apply colored coatings according to CI color specifications or for decorative purposes by manual and automated airbrush processes.
- spray lacquer application with airbrush technology
- manual and automated painting processes
- color selection according to RAL/Pantone
- clean room with extraction system
- large painting chamber and drying room
- full or partial paint finishes
Laser Engraving
Our fully automated laser marking system is integrated into the production processes with robotic feeding. This ensures fast throughput with large quantities and consistent quality. Laser engravings are possible, ranging from simple serial numbers (continuous) to QR/bar codes (for perfect tracing and counterfeit protection) to decorative and enhancing logos, even in 3D.
- fully automated laser system
- robotic feeding in the production process
- batch sizes up to 100,000 pieces per day
- 2D and 3D engraving (efficient or noble)
- automatically consecutive serial numbers
- barcodes/QR codes for easy tracing
- customizations
Quality Control (QC)
Our workpieces are checked for accuracy and compliance with the respective requirements in each process step. This is done according to the basics of high-end measurement technology to ensure that the workpiece has the required properties, such as dimensions, shape or surface quality. Both subjective and objective tests are carried out. Subjective testing is carried out by the examiner’s sensory perception without any auxiliary devices. It determines by visual and tactile testing whether, for example, burr formation and roughness on the workpiece are permissible. For objective testing, we use extensive precision measurement technology.
Precision Measurement Technology
Even during production, the drilling and milling machines automatically check both their own tools for wear and tear and the workpieces for compliance with tolerances. This is done by simultaneous control measurements during the milling process by tactile control measurements. In addition, our testers check the machine tests again after production using measuring microscopes and roughness measuring devices. First sample test reports are only generated based on the values determined here. We have been processing metal in the precision sector for over 30 years and offer the production of precision mechanical components.
- iconic design
- accessories
- high-end jewellery
- metal components
Test Methods
If this is part of our mandate, we will make sure that your products undergo a series of tests under laboratory conditions to ensure that the products can withstand the loads intended for them in the long term. We have already taken these requirements into account even in product development and all production processes, so that your products can withstand these tests.
The following tests -next to others- are offered:
- nickel release test (simulated corrosion, simulated usage)
- abrasion tests
- corrosion tests / climate change tests
- compliance with the REACh-regulation
- drop tests
- material analyses
- minimum number of function operations (e.g., open-close)
Assembly &
Picking
After your products have been produced and tested according to all requirements, the products are finally cleaned and then finalized until delivery. On request, we take care of all necessary steps from the assembly of individual components to an assembly group as well as packaging in decorative boxes for the end customer, picking and delivery.
Cleaning Techniques
Even if our production looks more like clean laboratories than factory halls, cleaning the workpieces may be necessary before further use. We have a wide range of possibilities for this:
- steam jet cleaning systems
- ultrasonic technology for industrial precision cleaning
- cavitation principle, microscopically smallest vapor bubbles adhere to dirt and are brought to the solution by ultra-frequent pressure fluctuations
- removes even the smallest particles up to particle size 1 micron
- environmentally friendly - energy-efficient water-based process
- fast - short turnaround times
- penetrating - cleans even complex structures with holes and channels
Assembly
After all required components have been produced, they are assembled by our production teams on site, if we are commissioned to do so. For this purpose, the individual components roll into the respective production areas on specially developed transport trolleys. Numerous tools and innovations that have been developed and even patented by our in-house team of specialists for these purposes help with the assembly. These include, for example:
- patented multi-component adhesive
- adhesive-free connection techniques
- special pressing tools
- automatic stone setting machines
- laser welding technology
Picking
In our shipping department, our teams pick every item ready for sale on request. All required labels, bar/ QR codes and accompanying documents are created and attached as intended. The sales packaging is supplied by our customers or we procure it just-in-time according to the requirements. We use extremely efficient and sustainable storage boxes in the warehouse system, which optimally protect the products and return them to us for reuse.
- partial or complete picking
- including bar/QR codes
- sales packaging provided or procured by us
- deposit system for unpacked components
- high picking capacities
- storage possibility on request
- ready to ship preparation
- customs clearance (if applicable)
- safety transports possible
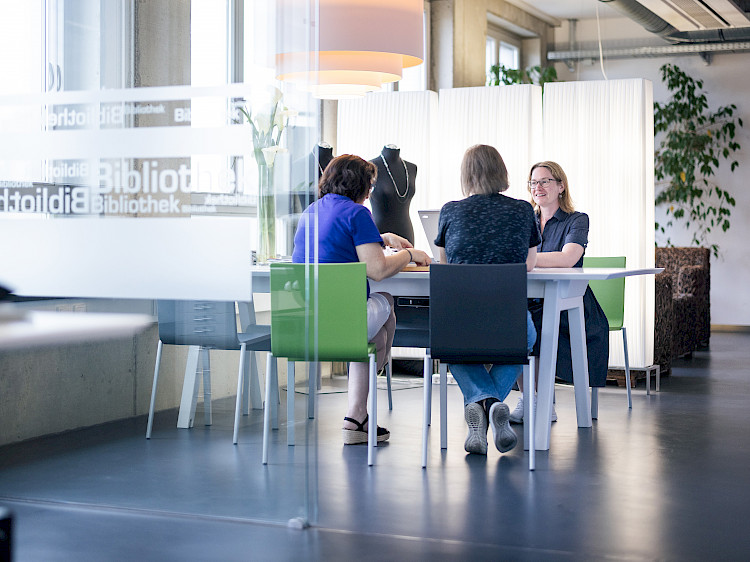
Do you have any questions?
We are here for you.
Whether technical details or general information on products and sales. We will be happy to help you by e-mail or telephone.
Tel. +49 (0)89 370 735 0